

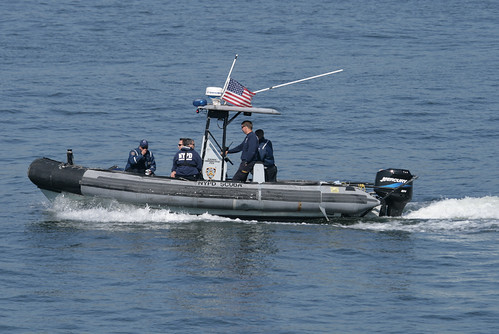
NYPD Zodiac Hurricane w/Scuba team, in New York, USA. May, 2008 , originally uploaded by Tom Turner - SeaTeamImages / AirTeamImages.












Oceanic/USA is a relatively new name on the dive scene. The company's former names and various products, however, we well known to a large segment of the diving population. Over the last decade, under the names of Oceanic Products, and later, Oceanic-Farallon, this company has gained an enviable reputation with divers as an innovator, manufacturer and distributor of diverse underwater equipment.
With all of their engineering development and precision manufacturing capabilities, in addition to their extensive experience in dive equipment, it is not surprising that Oceanic decided to produce their own regulator. Nor is it surprising that they arrived at such an innovative design. The Omega regulator is the result of Oceanic's research and development effort. As Bob Hollis, head of Oceanic/USA, indicated, the objective of this effort was to make a regulator that is reliable, sensitive and comfortable in use--so that breathing underwater would be as easy, smooth and natural as breathing normally above water. Autonomic is a word Oceanic likes to use in describing the new regulator's response. An antonomic response means the regulator, "breathes simultaneously with you, not after you-- no surge, no unpleasant feedback; just gentle, effortless breathing.'
The first stage is conventional is design and materials. It is based on the very popular and widely used balanced flowthrough piston design. This design was chosen because of its simplicity, dependability and high performance characteristics. Machined brass is used in the body and yoke screw and forged brass is used in the swivel yoke. All three pieces are triple chrome plated: that is, copper plating first, then one of nickel and finally one of chrome. The piston is stainless steel, with a Teflon coating to reduce friction and resist freeze-up when diving in cold water. Stainless is also used in the main spring. For a more precision seal the high pressure valve seat consists of micro-lapped, virgin Teflon (which means the Teflon seat has a very flat surface). The yoke is pressure rated for 4500 psi and by the end of this fall a DIN connection will be available with the same pressure rating. Additional features of this first stage include: a conical high pressure (inlet) filter, for increased filtering capacity; an intermediate pressure range of 135 to 145 psi; two high pressure ports, on opposite sides of the body, and marked with 300 bar and 4500 psi; four low pressure ports spaced around the circumference of the swivel low pressure cap; and a solid rubber dust cap. Although the Teflon coating on the piston offers some protection from first stage freeze-up during cold water use, additional protection will be provided by an optional environmental protection kit, scheduled for sale before the end of the year.
The uniqueness of the Omega lies in the second stage, the design of which utilizes a very modern, adjustable, downstream, servo-controlled demand valve. This sounds like a mouthful, but is actually relatively simple in its operation. Under static conditions, air from the low pressure hose is prevented from entering the second stage by the main value. This valve consists basically of a thick, specially compounded neoprene rubber disk, which covers the main valve opening on the downstream side. At the center of this disk is a stainless steel insert, containing a small hole. Air can pass through the hole into the control chamber behind the disk, until the pressure is equalized on both sides. Since the control chamber has a larger diameter than the main valve opening, the air on the control chamber side exerts a greater closing force on the disk, because it is acting on a larger surface area of the disk. Hence, when the pressure in the control chamber is equal to the intermediate pressure in the hose, the main valve will remain closed. It is interesting to note here that the air pressure itself keeps the main valve closed-- no spring is needed. At the other end of the control chamber is a small port, which, under static conditions is closed off by a rubber pad molded onto the end of the demand lever. Together, the port and the rubber pad form the orifice and the seat, respectively, of the servo-valve. Because the port is so small, only a very small spring is needed to keep this servo-valve closed. If the demand lever is depressed by even a slight amount, the servo-valve will open and air will escape from the control chamber faster than it can enter through the hole in the disk of the main valve. The resulting drop in pressure within the control chamber allows the higher pressure air on the upstream side of the disk to bulge the disk out, away from the main valve seat. As the disk becomes more concave in shape, supply air can pass through the main valve and into adjacent wedge-shaped openings leading to the second stage, and thence to the mouthpiece. If the servo-valve is held open, as in cases of continued demand by the diver, pressure in the control chamber will continue to decrease, causing the disk to bulge out further, uncovering a greater portion of each triangular opening and, therefore, releasing even more air to the mouthpiece. This provides air in a smooth, proportional response to demand.
The stacked, diaphragm/exhaust valve arrangement is another interesting aspect of this second stage. A flat, plastic, spoked wheel, about 1.6 inches in diameter, forms the central component. A mushroom type exhaust valve is secured to the top of this wheel and seals against its rim. The diaphragm, which looks like a narrow, convoluted ring, is attached at its inside perimeter to the outer edge of the wheel, while the outside perimeter of the diaphragm is clamped into place in the second stage case by the screw-in, plastic diaphragm/exhaust valve cover. With this design, a diaphragm with an effective diameter of 1.7 inches (the wheel functions as part of the diaphragm) and a large, 1.5 inch diameter exhaust valve can be fitted into a very small space. An adjustable set screw, which contacts the end of the demand lever, is at the center of the wheel. With only brief instruction, this set screw can be adjusted by the diver to custom tune the regulator to just about any sensitivity. The purge button is flush mounted, spring loaded and held captive at the center of the diaphragm/ exhaust valve cover. It is easy to reach at the end of the second stage.
Non-corrosive materials are used throughout: critical metal parts are stainless steel; other metal parts are chrome plated brass; Noryl , a plastic developed for marine applications, is used in all of the rigid plastic parts, including the case, exhaust cover, main valve seat, etc.; the standard mouthpiece and main valve disk are of neoprene; and the exhaust valve, diaphragm and optional mouthpiece are of silicone rubber. Incidentally, both mouthpieces come with moldable bite tabs for more comfort and less jaw fatigue during dives. Besides corrosion resistance, the use of plastic results in a light weight (only six ounces) second stage, and offers some thermal insulation, resisting cold water freeze-up.
Oceanic/USA's Omega retails for $250 and comes with a lifetime, limited warranty. To ensure each new owner's satisfaction, Oceanic conducts 100 percent performance tests on its regulators on a flow bench, prior to shipment. Routine care should be the same as that given any good regulator.
And my evaluation? In a word, "satisfying!' I dove with this unit on four separate occasions under varying conditions, ranging from cold water at about 90 feet, to warm water (for California, anyway) at depths of 10 to 15 feet, from calm to choppy surface conditions, and with tank pressures from 2200 psi to nearly empty. The Omega performed very well. Regardless of depth, it supplied as much air as I could possibly accept without being excessive. Inhalation resistance was quite low as was exhalation resistance. Free-flowing was not a problem: self-stopping, in fact, except when the exhaust was lower than the mouthpiece, the latter pointed up, and the stage full of air or purged. My usual contorted positions produced no unusual characteristics. Popping, stuttering and instabilities were not noticed, even shallow or when inhaling through clenched teeth. The only idiosyncrasy I recall was a very slight water leakage when tilting my head to the left, so that the exhaust valve was pointed upward. And, this wasn't bad.
It appears Oceanic has met their goal: smooth, comfortable breathing in a scuba regulator. By design the Omega should be dependable. And, in my opinion, it is a high performer. Try the Omega. Most likely you'll be satisfied too!
Photo: Top: The uniqueness of the Omega regulator lies in the second stage which uses an adjustable, servo-controlled demand valve (see diagram). The first stage (above middle) has four low pressure ports around the low pressure cap.
Source Citation
Coz, George. "Oceanic-USA Omega." Skin Diver Nov. 1983: 34+. General OneFile. Web. 21 Jan. 2010.
Gale Document Number:A2988565











No comments:
Post a Comment